3D printing has a very obvious speed advantage in small batch production and in the development of certain types of projects, such as automotive, aerospace, aviation, military, train, motorcycle, ship, mechanical equipment, water pump, and ceramic, etc.?
A variety of traditional casting products that are difficult to produce can now be produced by 3D printing?such as 0.5mm turbine blades, various internal cooling oil passages, and various structurally complex castings.?
For art pieces, various types of molds for mass production can also be widely used.
3D printing boosts casting incustry
Vacuum Casting
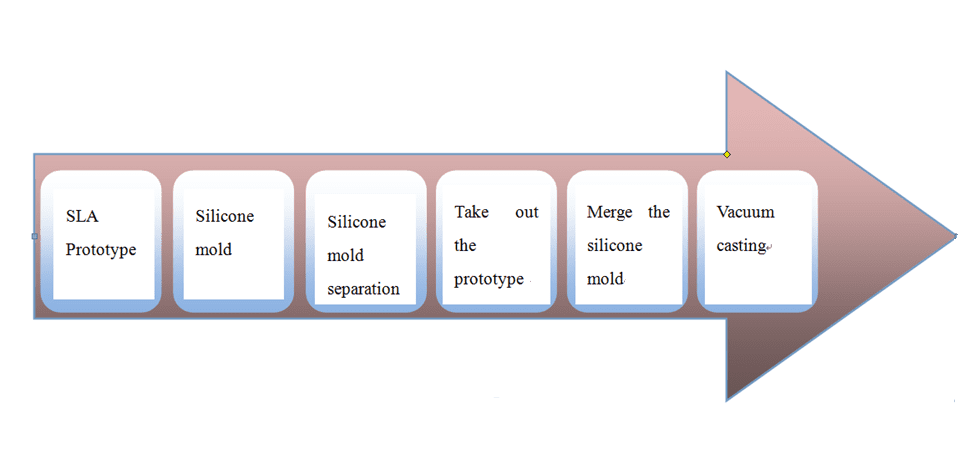
Based on the application of RP technology, the new product development line, which used the RTV silicon rubber molding and vacuum?casting, has now widely applied to the field of automobile, electronic and medical field.


RIM: Low-pressure reaction injection molding(Epoxy molding)
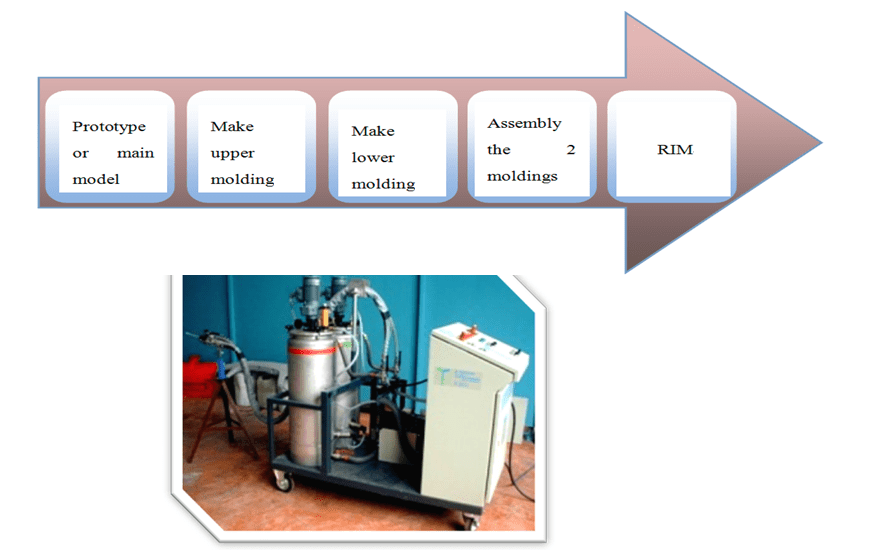
RIM is a new process applied to the production of rapid moldings. It is a mixture of two-component polyurethane materials, which are injected into a rapid mold under normal temperature and low pressure and formed by chemical and physical processes such as polymerization, crosslinking and solidification of materials.
It has the advantages of high efficiency, short production cycle, simple process and low cost. It is suitable for small-scale trial production in the product development process, as well as small-volume production, simple structure of the cover and the production of large thick-walled and uneven thick-walled products.
applicable molds: resin mold, ABS mold, aluminum alloy mold
casting material: two-component polyurethane
material physical properties: similar to PP / ABS, the product has anti-aging, strong impact resistance, high degree of fit, easy loading and unloading
The working principle of RIM low-pressure perfusion molding is as follows: the pre-formed two-component (or multi-component) liquid raw materials are fed into the mixing head through a metering pump at a certain ratio, and then continuously poured into the mold to form a reaction solidification molding. The ratio adjustment is achieved by a change in pump speed, which is controlled by the unit discharge amount of the pump and the injection time.
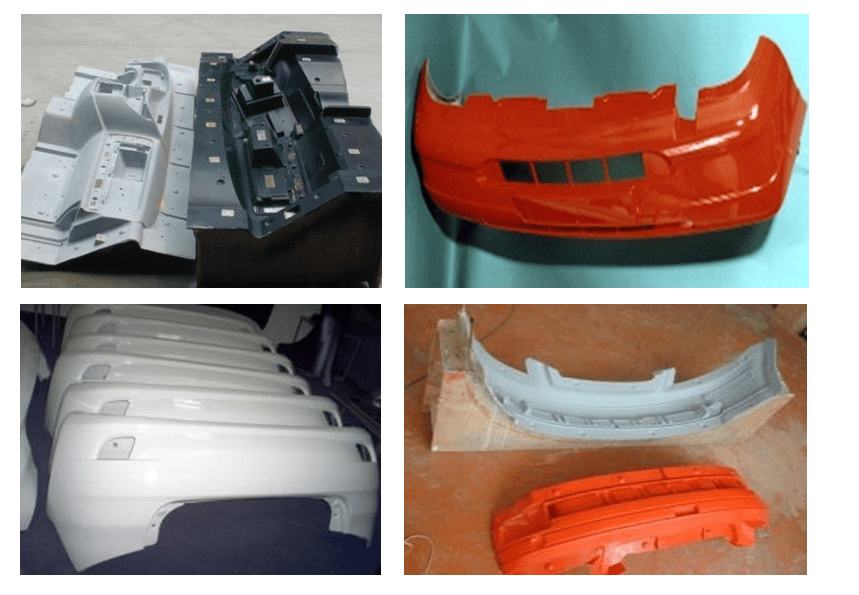
Carbon fiber / fiber reinforced plastics(FRP) vacuum introduction
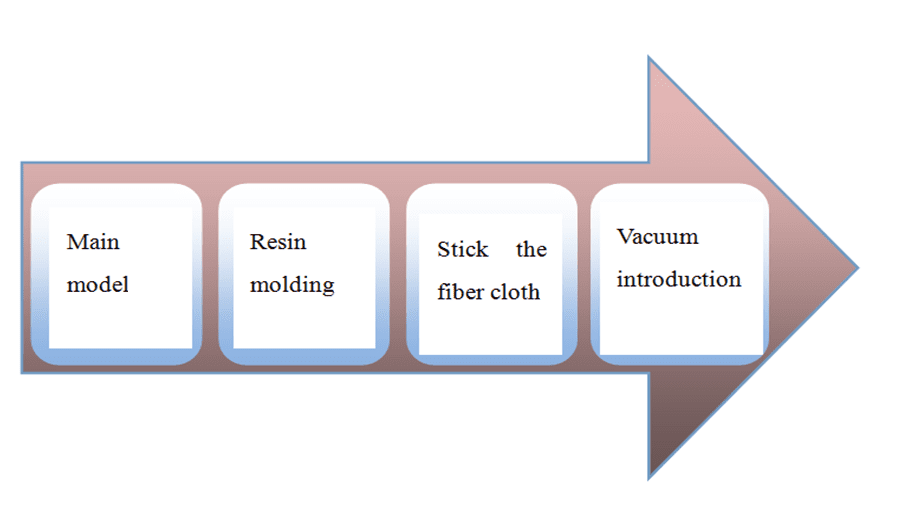
The basic principle of the vacuum introduction process refers to laying glass fiber, glass fiber fabric, various inserts, release cloth, resin permeable layer, laying resin pipeline and covering nylon (or rubber, on the cured gel coat layer). Silicone) flexible film (ie vacuum bag), the film and the periphery of the cavity are tightly sealed.
The cavity is evacuated and the resin is injected into the cavity. A molding process in which a resin is impregnated along a resin pipe and a fiber surface under vacuum to impregnate the fiber bundle at room temperature or under heating.
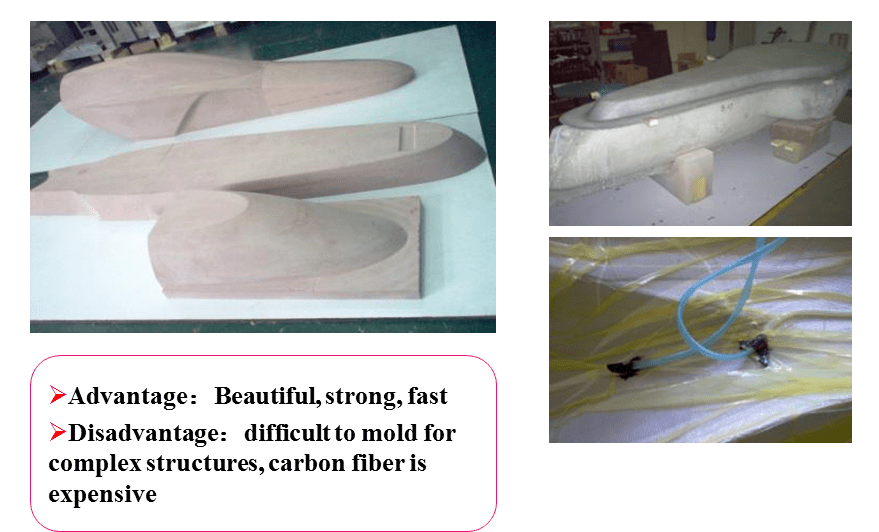
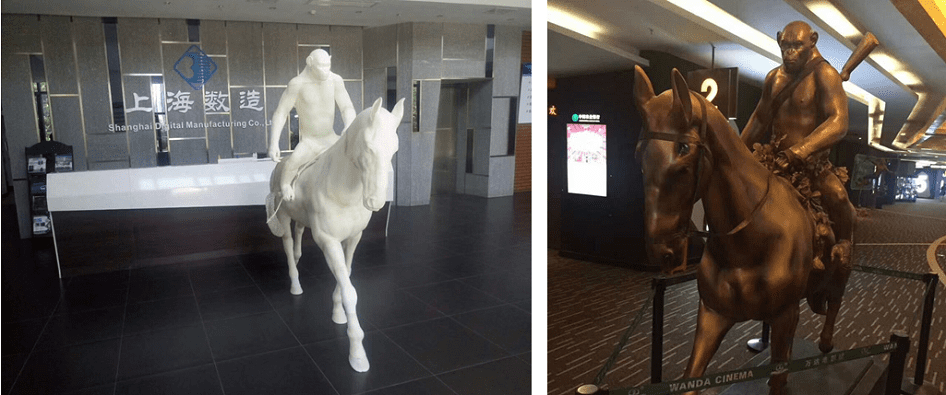
Rapid casting
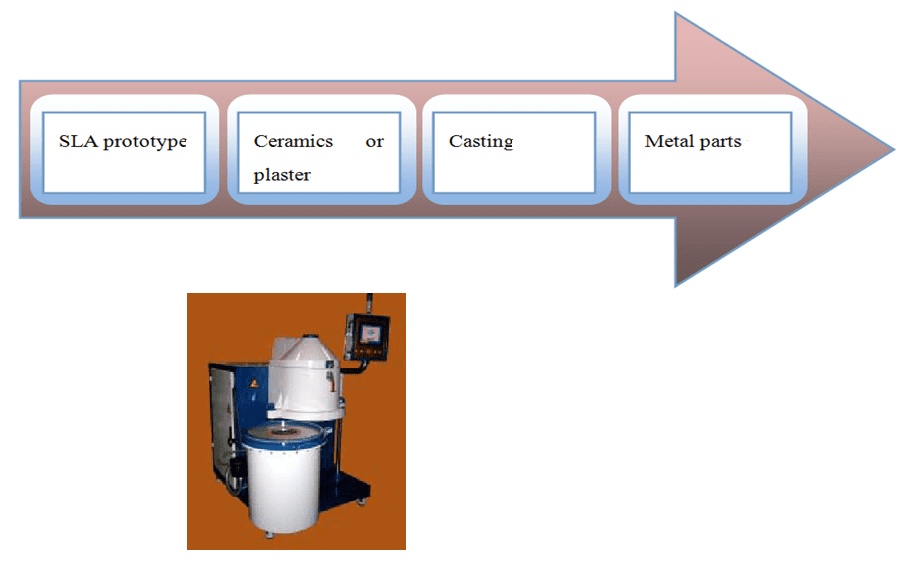
The combination of 3D printing technology and traditional casting technology has resulted in rapid casting technology. The basic principle is to use the 3D printing technology to directly or indirectly print the lost foam, polyethylene mold, wax sample, template, mold, core or shell for casting, and then combine the traditional casting process to quickly cast metal parts.
The combination of 3D printing technology and casting process gives full play to the advantages of fast 3D printing, low cost, the ability to manufacture complex parts and cast any kind of metal, and is not affected by shape and size, and low cost. Their combination can be used to avoid weaknesses, greatly simplifying and shortening the process of lengthy design, modification, redesign to molding.



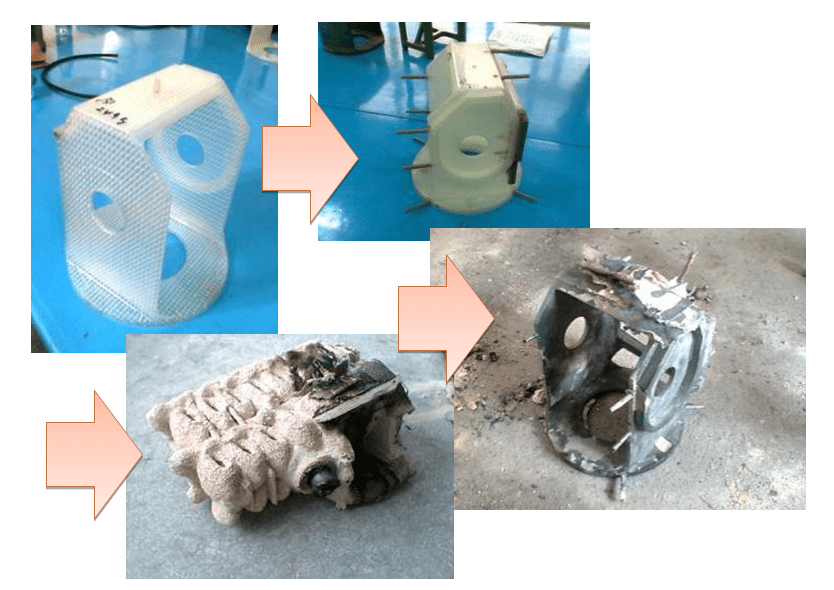


Investment casting
Investment casting refers to a relatively new method of casting metal, also known as full mold, vaporization, and cavityless casting. The prototype is made of foam (FOAMED PLASTIC) and is usually expanded polystyrene. The positive mold is filled with the cast sand (FOVNDRY SAND) to form a mold (MOLD), and the same is true for the negative mold. When the molten metal is injected into the mold (ie, the mold made of polystyrene), the foam evaporates or is lost, leaving the negative mold of the foundry sand filled with molten metal. This method of casting was later adopted by the sculptor community and is now used in industrial manufacturing.
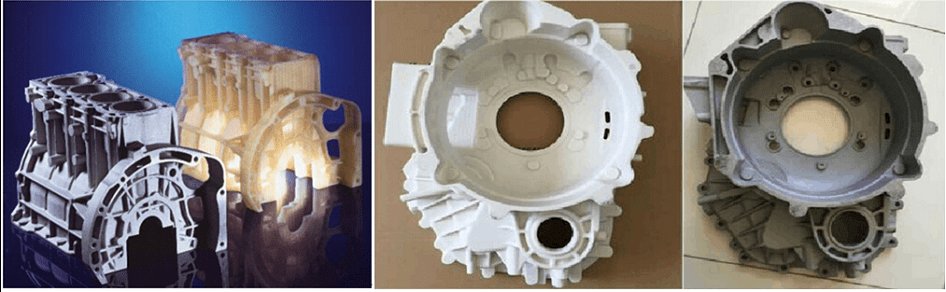
SL 3D printer recommended
Large size of SL 3D printer is recommended, such as 3DSL-600Hi with build volume of 600 *600*400 mm and bigger machine of 3DSL-800Hi with build volume of 800*600*550mm.